The Reelwell Drilling Method (RDM) is a new technology developed to solve certain drilling problems and improve the operation margin for various applications.
The technology uses a specially designed dual drillpipe (DDP), shown in Fig. 1 above, that has two flow channels, one for the flow of drilling fluid into the well down to the bit and the other for the return flow of fluid from the bottom of the well back to the surface.
Developed in Norway, the RDM has been field tested at various locations in the past several years. The technology has features for pressurized mud cap drilling (PMCD), managed pressure drilling (MPD), and extended reach drilling (ERD). The RDM enables
- PMCD with cuttings return
- MPD with a constant well pressure profile
- ERD with reduced torque and drag, no equivalent circulating density (ECD) in the wellbore, and no cuttings in the hole
The DDP is available in 6⅝-in. steel and 5⅞-in. to 7½-in. aluminum pipe diameters. With a pressure rating of 5,000 psi, the DDP contains a concentric inner pipe with a stab-in connector and is handled in the same way as a conventional drillpipe.
The RDM can be adapted to a standard drilling rig, with the following tools and arrangements:
- A top drive adapter—a swivel directing the fluid return through a second standpipe and mud hose
- An inner pipe valve—a bottomhole assembly (BHA) tool for the isolation of the drillstring during connections
- A flow control unit—a skid with a control valve system for flow and pressure control
- A rotary control device—a standard tool at the blowout preventer for MPD
The RDM uses standard BHA components and drill bits, and the tools operate on reduced flow rates.
Case Study: Middle East
An RDM field trial was performed at an onshore field in the Middle East during December and January. The goal was to qualify the RDM in a 12¼-in. hole section for the verification of efficient hole cleaning, constant bottomhole pressure, avoidance of formation damage, and compatibility with a rotary steerable system (RSS) and mud telemetry.
The 12¼-in. section was drilled with an 8.9-lbm/gal drilling mud. The well pressure was controlled by a pressurized mud cap with an equivalent mud weight of 10.2 lbm/gal. Reelwell’s Drillsim drilling simulator was used for the preparation and in training the rig crew and the operator’s personnel. The section was drilled with an RSS and downhole pressure monitoring using conventional mud pulse telemetry.
The operation successfully showed
- PMCD with cuttings return
- Efficient hole cleaning at low flow rates
- Minimum fluid loss
- Compatibility with an RSS and a conventional measurement-while-drilling system
The trial confirmed the predicted behavior of the system and the achievement of penetration rates according to plan. The downhole pressure could be monitored by the downhole pressure sensors and the well annulus casing pressure during the operation. A second mud pump and choke arrangement was used to keep the casing pressure constant during connections (Figs. 2a and 2b). The procedures to obtain stable downhole pressure control were verified.
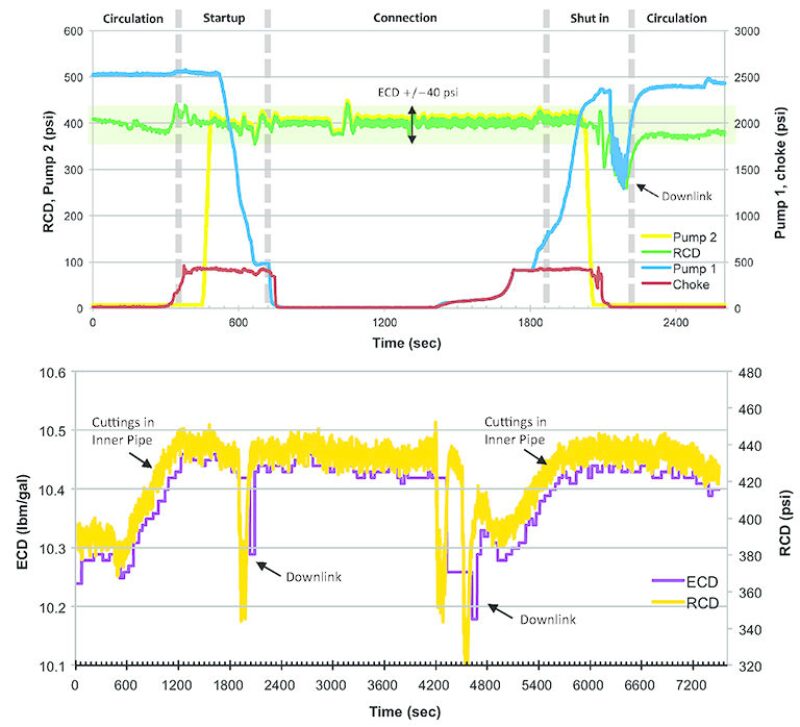
The operation was ended because of a leak in the inner pipe. The cause was identified and the pipe is being upgraded. All other tools and arrangements proved reliable in operation, according to the specifications. The well was completed by conventional methods, as planned.
The main results are summarized as follows:
- A vertical kickoff with a 3°/100 ft build rate, as per the drilling program
- A drilled interval by the RDM of 5,700 ft to 6,300 ft in measured depth
- A rate of penetration at 30 ft/hr to 45 ft/hr, as per the drilling program
- Efficient hole cleaning at a mud flow rate of 200 gal/min to 220 gal/min
- A stable well pressure during drilling and connections
The operation showed a successful new approach to PMCD, which differs from the conventional approach by cleaning the hole during the operation. This is possible because the RDM enables the execution of good hole cleaning in the separate return flow channel, even with low return flow rates. For applications that are prone to fluid loss, this ability is an important improvement.
The operation proved the system’s ability to keep the downhole pressure approximately constant during all operational steps, including the starting and stopping of the mud pumps during connections. In addition, the system proved that a simple, reliable continuous monitoring of the downhole pressure could be achieved and recorded by surface readings.
Looking Ahead
The next step is to prove new features of RDM related to ERD, where many challenges exist.
Torque and drag can be a limiting factor for ERD wells. Reelwell has developed a new buoyancy technique to overcome this challenge by using a low-density active circulating fluid and a high-density fluid in the well annulus outside the drillpipe. When using the specially developed aluminum drillpipe, the buoyancy can enable significant torque and drag reduction.
ECD can be a limiting factor for ERD wells. RDM provides a potential remedy in which the ECD is hidden inside the inner pipe, i.e., the well only experiences the pressure from the static fluid in the annulus. The constant pressure gradient is an advantage when drilling through sections with a narrow pressure window, and when increasing the casing shoe depth for a well section. The constant pressure gradient also prevents the washouts of weak zones and thereby leads to improved wellbore stability.
Reelwell is conducting a joint industry project on ERD this year, supported by the Research Council of Norway, Total, Petrobras, and RWE Dea. In collaboration with Halliburton in an onshore ERD well in Texas, the project aims to demonstrate the unique ERD capabilities described above.
Hole cleaning is a challenge in horizontal wells. RDM provides superior hole cleaning because the cuttings are transported at high speed from the top of the BHA through the return channel back to the surface. The bottom-up time is very short. In practice, the hole will always be clean when using the RDM.
Another significant difference between the RDM and conventional drilling is the ability to perform a formation evaluation (FE) from the bit cuttings during drilling. The cuttings move at high speed through the return channel back to the surface, without exposure to mechanical grinding and mixing. This allows a precise FE from a cuttings analysis, which can reduce the requirements for coring, well logging, and the use of advanced logging-while-drilling tools.
Recommended Additional Reading
SPE 119491 Reelwell Drilling Method by O. Vestavik, Reelwell, et al.
SPE 137821 New Approach to Improve the Horizontal Drilling Reach by O. Vestavik, Reelwell, et al.
SPE 145599 Deployment of Reelwell Drilling Method in a Shale Gas Field in Canada by M. Belarde, Shell Canada, et al.
SPE 163463 Extended Reach Drilling—New Solution With a Unique Potential by O. Vestavik, Reelwell, et al.