As the task of finding and producing hydrocarbons becomes more difficult, complex, and costly, the number of universities focusing on finding solutions has risen. Whether the frontier is heavy oil, deep water, or remote locations, efforts within academia are under way to solve the next generation of technical challenges confronting hydrocarbon E&P operations. Because many noteworthy research and development (R&D) efforts exist at universities all over the world, the intent is not to cover all of them but to present a sampling from many geographical locations. Part 2 of this article will appear in the October issue of JPT.
The Pennsylvania State University, Pennsylvania, USA
The Pennsylvania State University was chartered in 1855 as Farmers’ High School, located in Centre County, Pennsylvania, USA. In 1862, the school officially changed its name to the Agricultural College of Pennsylvania. The US Congress passed the Morrill Land-Grant Act in 1862. The act donated federal public land to each state. When each state sold the land, the proceeds were to be used for the endowment, support, and maintenance of at least one college where not just traditional classical studies would be offered, but agriculture and engineering would be taught in a new, practical, scientific manner.
Competing with five other schools, the Agricultural College received the Pennsylvania land-grant endowment in 1863 when the state legislature designated the college the land-grant institution of Pennsylvania. Penn State remains Pennsylvania’s only land-grant institution.
The school’s name was changed to Pennsylvania State College in 1874. The college was elevated to university status in 1953 and renamed The Pennsylvania State University.
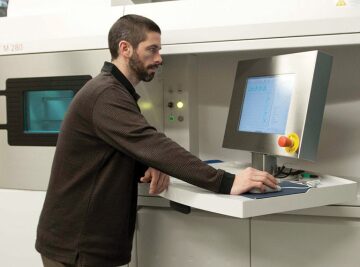
Penn State has taught petroleum-related classes since 1896 and today has an active upstream research program including studies on such topics as fluid dynamics, reservoir engineering, and improved oil and gas recovery. In addition, Penn State’s College of Earth and Mineral Sciences established the Institute for Natural Gas Research in 2013, and several Penn State colleges fund the Penn State Marcellus Center for Outreach and Research, the university’s education and research initiative on unconventional gas plays.
Petroleum R&D and the Applied Research Laboratory
Penn State is home to the Applied Research Laboratory (ARL). ARL is run by a combination of approximately 900 full-time employees and 30 graduate students, and provides financial support to around 350 students during the course of a year through both graduate and undergraduate student programs. While the research complements the studies of the students, ARL functions independently from Penn State’s regular educational mission.
Only recently has the ARL become involved in petroleum R&D.
ARL was established in 1945 by the US Navy to conduct studies on naval and defense topics. The facility is designated by the United States Department of Defense as an official US Navy University-Affiliated Research Center and maintains a long-term strategic relationship with the Naval Sea Systems Command and Office of Naval Research.
According to Timothy Bair, director of Penn State’s Institute for Manufacturing and Sustainment Technologies, it was the flurry of activity in the nearby Marcellus shale that spurred ARL to leverage its existing R&D efforts to solve oilfield challenges, starting around 2008.
Additive Manufacturing
One strength ARL has imported into the hydrocarbon realm is its experience with technology transfer. A relevant example is ARL’s work on additive manufacturing. In a broad sense, this concept is not uncharted territory for industrial manufacturing and engineering, but there is still room for new applications.
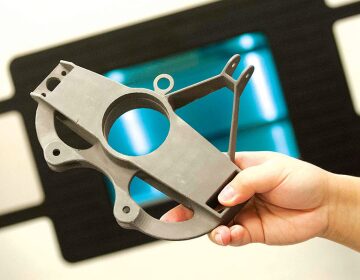
The process is probably more familiar to the general public as a type of 3D printing. Instead of filling a mold with molten plastic or metal, or subtracting a refined shape from a larger block of material, 3D printing makes 3D solid objects from a digital model. Additive manufacturing creates an object by laying down successive layers of material. One approach to 3D printing uses a laser to sinter granular material (i.e., powder) into a solid. Electron beam melting is a similar type of additive manufacturing that creates a solid object by melting metal powder layer by layer with an electron beam in a high vacuum.
Manufacturers and programmers often showcase these printers by creating simple trinkets or paperweight-type objects, using a nylon-based powder. On a practical level, this type of small-scale manufacturing can be used to quickly create prototypes and models for engineering and design purposes. However, while nylon and other polymers are sufficient for some applications, when high strength and integrity are required, as is the case in oilfield environments, materials like metals and ceramics must often be used.
According to Timothy Eden, head of ARL’s Materials Processing Division, the standard of quality required in additive manufacturing jumps up drastically when it is used for fabricating metal products. To become an industry norm and to be embraced on a large scale, the process must provide—on a consistent basis—material integrity comparable to that of conventionally manufactured (i.e., machined) products.
Net shape is also a concern. Will metal parts manufactured this way always require extra machining, or can they come out ready to use? ARL is still answering these questions. “One day we hope that every one of the drilling companies or completion companies has in the back of a truck one of these machines that has the capacity to make a part up to a certain size, say a couple feet in any one direction,” said Eden. Having the ability to create a part on site—especially if the operator is at a remote location—could greatly reduce supply chain costs and minimize nonproductive time.
Unmanned Underwater Vehicles
Another research area that overlaps with the needs of the upstream oil and gas industry is ARL’s work with unmanned underwater vehicles (UUVs), which researchers essentially build from scratch. “They design everything from the propulsor, the shell, the guidance system, the sensor suite, systems for data collection—that’s all done at ARL,” said Eden.
Penn State’s current crop of UUVs features a modular sensor package design, which allows for easy installation and removal of different sensor modules based on operational requirements. Some common applications for UUVs include subsea geophysical mapping, and inspection for leaks, damage, and other hazards.
Among other on-campus laboratories and testing facilities, ARL operates the High-Pressure Test Facility—located in the ARL building—which simulates deep ocean environments. ARL conducts scale-model testing of underwater vehicles and their components at its many test facilities, including various water tunnels, a quiet pump loop, a glycerin tunnel, an acoustic reverberant tank, and a flow-through anechoic chamber. Such testing is possible using ARL’s computer-aided design and manufacturing capabilities, five-axis numerically controlled milling machines, and coordinate-measuring machines to create models. Engineers and technicians at ARL’s Keyport Test Site, located in Keyport, Washington, maintain and operate a small fleet of ARL test vehicles for testing and demonstrating a wide variety of undersea technologies. ARL also operates its Deep Ocean Test Facility in Annapolis, Maryland, and smaller facilities elsewhere in Pennsylvania and in the states of Virginia and Hawaii.
University of Connecticut, Connecticut, USA
The University of Connecticut (UConn) was founded in 1881 in Storrs, Connecticut, as an agricultural college. Today the university has a wide curriculum including geology, engineering, and chemistry, but lacks a petroleum engineering degree program.
The situation is similar for the university’s research: While there are many peripherally related areas, there is no concerted upstream oil and gas research effort.
However, in 2014, UConn sent representatives to the annual Offshore Technology Conference in Houston, Texas, to showcase work its advanced-degree students are doing on subsea telemetry that could benefit the oil and gas industry.
Underwater Acoustic Modems
Since 2006, UConn’s School of Engineering has conducted underwater research. One of these projects is a new variant of underwater acoustic modem: a device that transmits subsea data to the surface using acoustic waves, which in some cases might eliminate the need for expensive and unwieldy subsea cables.
“Acoustic modems are not exactly a new technology; there’s a lot for sale on the market already,” said PhD candidate and UConn researcher Michael Zuba. “What makes the modems developed at UConn different is, first, we use a different modulation technique called orthogonal frequency-division multiplexing [OFDM].”
OFDM
Like the subsea modem, OFDM itself is not a new discovery; however, its use in an aquatic medium is novel. UConn’s aquatic sensor network technology (AquaSeNT) modem divides the data and transmits them as multiple, low-modulation subcarrier sonic waves, spaced extremely close together, which is known as frequency-division multiplexing (FDM).
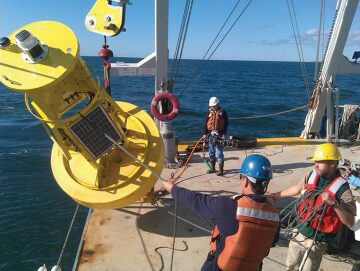
OFDM is different from conventional FDM because the orthogonal shape and spacing of OFDM waves prevent them from interfering with each other (a phenomenon called crosstalk) despite their extreme proximity. This allows the waves to carry a greater amount of data than other techniques. OFDM has been used in terrestrial radio applications since the 1970s.
The original challenge to using OFDM modulation offshore is the fact that the orthogonality gets distorted when waves travel through an underwater channel. UConn researchers solved this problem by applying proprietary signal processing and algorithms which compensate for that distortion.
Modem Performance
UConn’s AquaSeNT modems send data at a higher rate than is conventional for a subsea modem—2 to 5 more bits of information per second than competitors, depending on operating conditions. Zuba said that one day the OFDM modems could be able to transmit at optimal rates over distances as great as 50 km (31 miles); currently, the modems can transmit over a distance of 4 km (2.5 miles).
Subsea modems like these have numerous oil and gas applications, including monitoring of subsea production, control of autonomous underwater vehicles (AUVs), and operation of subsea valves, to name just a few.
The US National Oceanic and Atmospheric Administration (NOAA) has tested the modems in Chesapeake Bay, offshore US states Maryland and Virginia. The modems were attached to sensors on the bay’s floor, and they sent environmental data from the sensors to buoys on the surface, which used more powerful transmitters to send the data to cellular towers on shore. NOAA was able to get more reliable performance using OFDM modems compared with other modems they had used in the past.
Since 2012, UConn has sold the modems on a small but commercial scale through a startup company called AquaSeNT. The company has an off-campus location where employees assemble, test, and ship the units. Basic components of the modems—such as the underwater enclosure, or shell—are fabricated outside of Storrs at a manufacturing facility.
Smart Ocean Technology Research Center
In addition to AquaSeNT, UConn also has light involvement, through intercollegiate research, in some other potentially upstream technologies. Over the past year, UConn has been preparing for the official launch of the Smart Ocean Technology Research Center (SOTC), a joint research effort with the University of Washington for the purpose of developing new marine technologies.
SOTC is funded by the US National Science Foundation’s Industry & University Cooperative Research Program (I/UCRC) and member companies and organizations, which can buy into the center at associate and full levels. Each year, I/UCRC will provide USD 75,000 to the two universities for administrative costs; research budgets will be footed by dues-paying member companies and organizations. Some proposed SOTC projects include adaptive cleaning of oil spills using AUVs, subsea robotics, and microbial fuel cells.
University of Cyprus, Nicosia District, Cyprus
The University of Cyprus (UCY) was formed in 1989 and admitted its first class in 1992. It is based in Nicosia, the capital city of Cyprus. UCY only recently started offering petroleum-related degrees when nearby offshore discoveries in the Levant basin and the Eastern Mediterranean created enthusiasm in the region.
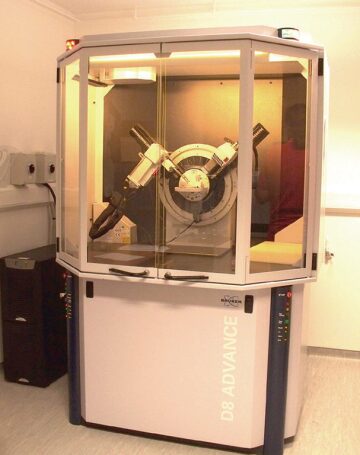
UCY started offering a master’s degree in petroleum engineering in September 2013 and currently has 24 graduate students enrolled in the program. And despite having a young program, UCY has an active student SPE chapter. Over the next few years, the university intends to significantly expand its oil and gas education and research efforts, including plans for an undergraduate degree in petroleum engineering and a dedicated department.
Interdisciplinary Approach to Oil and Gas Research
Because a petroleum department does not exist yet, the university is conducting research through an interdisciplinary approach. Multiple UCY Engineering School (established in 2003) subgroups are focusing on different facets of oil and gas based on their respective strengths. According to Panos Papanastasiou, UCY professor of petroleum geomechanics, the most active group at the moment is UCY’s Department of Civil and Environmental Engineering, which is leveraging its preexisting geomechanics capabilities to create computer models for studies on wellbore stability, sand prediction, hydraulic fracturing, and CO2 capture and storage.
Plans for UCY’s civil engineering unit also include using computer geomodeling to create an overall mechanical Earth model (MEM) of the entire Eastern Mediterranean region. A Levant MEM will help enhance understanding of the direction and magnitude of in-situ stresses, pore pressures, and rock-fabric fields—aiding present and future hydrocarbon exploration in the area. The university’s Department of Mechanical Engineering has also started work on rheology studies, which will serve as a foundation for future drilling fluids projects.
UCY Geophysics Laboratory
UCY has a fully equipped geophysics laboratory, according to Papanastasiou. Some of this equipment comes from the established geomechanics subgroup of the university’s Department of Civil and Environmental Engineering. The following are some of some of the laboratory’s most important pieces of equipment:
- Bruker’s D8 Advance X-ray diffraction unit
- Energy-dispersive X-ray spectrometer
- Micromeritics’ mercury intrusion porosimeter
- JEOL USA Inc. scanning electron microscope
- Microdestructive analysis equipment
- Hassler-cell permeameters
- Ultrasonic pulse velocity test equipment for measuring rock elasticity
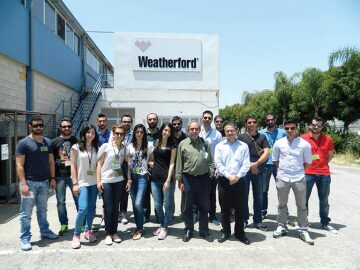
Current and Future Research
Currently, UCY’s petroleum research involves five faculty members and 15 students spread throughout various departments. The university’s activities are funded primarily by the Cyprus Research Foundation—a body set up by the Cypriot government in 1996 to promote scientific study in Cyprus. CYU has only a small amount of financial support from private industry, but much like the region itself, the university aims to attract more in the coming years.
In July 2014, UCY signed a memorandum of understanding with Texas A&M University to cooperate on matters of petroleum research and education and is in the process of planning joint petroleum education programs with several European universities.
Charles Darwin University, Northern Territory, Australia
Charles Darwin University (CDU)—formed in 2003 after 50 years of development, name changes, and mergers—is currently the only higher learning institution in Australia’s sparsely populated, 1.5-million-km2 Northern Territory. One of CDU’s missions is to help avoid brain drain and retain talent that might otherwise leave the territory in search of educational opportunities in more urban areas of Australia.
CDU is home to the North Australian Centre for Oil and Gas (NACOG), which aims to supply training and education together with research capabilities targeted at the specific needs of oil and gas operations and development in the region. The Northern Territory is adjacent to several natural gas discoveries in the Timor and Arafura seas.
The two R&D areas NACOG currently specializes in are corrosion engineering and multiphase flow.
Corrosion Engineering
Corrosion engineering is a study particularly relevant to the Northern Territory because of the detrimental effect the northern end of the territory’s climate—with its wet season (October through April) and tropical environment—can have on exposed metal structures.
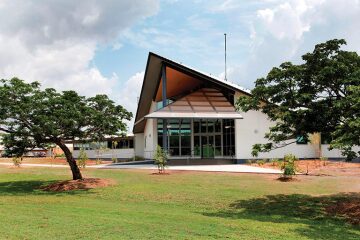
Krishnan Kannoorpatti, CDU associate professor, said preliminary studies by NACOG have shown corrosion of aluminum products in the Northern Territory to be approximately six times more intense than in other parts of Australia. The main culprit is a process called microbiologically influenced corrosion (MIC). MIC occurs when the metabolic processes of certain bacteria growing on or around metal surfaces make the surrounding environment acidic, which over time results in corruption and weakening.
NACOG’s corrosion program also studies the prevention of corrosion in hardfaced metals. Hardfacing is a process by which one metal is reinforced through the welding of another, often stronger, metal on top, either preemptively to prevent wear or after wear has occurred. The center is currently investigating the vulnerability of hardfaced metals to high-temperature and high-electrochemical-potential conditions.
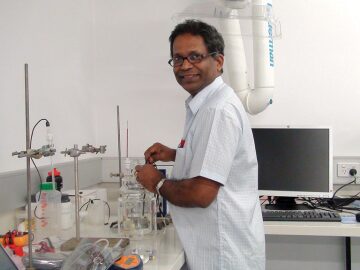
Assessment, testing, and inspection services are available through NACOG in the following areas:
- Corrosion measurement
- Electrochemical testing
- Stress corrosion cracking
- Corrosion fatigue
- Microbial corrosion
- Computer modeling
- Coatings analysis and inspection
- Weld testing and inspection
- Welding and surfacing
- Failure analysis
- Cathodic protection
Multiphase Flow
CDU also has the capability for researching multiphase flow and phase behavior. Central to this research is the full-vision sapphire high-pressure PVT (pressure/volume/temperature) cell. The PVT cell allows petroleum fluids to be studied and visualized at varying pressures and temperatures through simulating the conditions of petroleum fluids inside oil and gas reservoirs, pipelines, and process plants. Recreating these conditions allows researchers to investigate production optimization methods; hydrate formation, prevention, and control; and CO2 separation and capture.
The PVT cell’s many capabilities include the following: data acquisition software that automatically logs all variables; multiple sampling points before, during, and after experiments that allow for precise control of the composition and analysis of equilibrium phases inside the cell; and a digital camera that visually monitors changes inside the cell. Gas and oil can be analyzed for phase separation conditions to 0.1°C and 0.1 bar accuracy.
NACOG’s industry, government, and university partners include Clean Energy Fuels Australia; CO2 CRC for Greenhouse Gas Technologies; ConocoPhillips; Eni; Energy Centre, Robert Gordon University, Aberdeen, Scotland; Inpex; Northern Territorial Government; and Total.
University of Calgary, Alberta, Canada
The University of Calgary (U of C) was officially founded as its own distinct institution in 1966, 2 decades after opening as the Calgary branch of the University of Alberta in 1945. The university’s Geoscience Department has existed since 1963 and receives approximately CAD 5 million each year in research grants.
The Geoscience Department employs 76 full-time faculty and staff, with approximately 200 graduate students aiding in research. If graduate and undergraduate students are included in the head count, the number of people in the department swells to approximately 1,000.
Centers of study include the Petroleum Research Group, Consortium for Research in Elastic Wave Exploration Seismology, Applied Geochemistry Group, and a hydrogeology program, among others.
CHORUS
One particularly relevant focus of the university’s geoscience department—given the world’s growing interest in Canada’s unconventional resources—is the study of bituminous sands and heavy oil, which are abundantly present in the province of Alberta. The Consortium for Heavy Oil Research by University Scientists (CHORUS) was formed in 2002 and consists of eight investigators and 10 graduate students who study heavy oil reservoir characterization and the effectiveness of different production methods. The consortium is supported by a group of 17 industry partners, including Schlumberger, Fugro-Jason Canada, and CGG/Veritas.
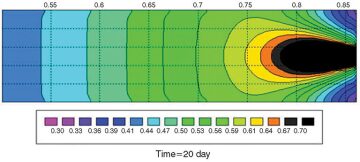
While CHORUS has applied for and received government grants in the past, industry support has been so strong that it has not needed to do so in recent times.
Hot Production
The consortium conducts research on both so-called “hot” and “cold” methods of heavy oil production. Hot methods produce heavy oil by reducing its viscosity with heat, which is usually generated by steam. CHORUS does research on cyclic steam stimulation, which consists of steam injection using a single vertical well to heat the reservoir, and also the more advanced method of steam-assisted gravity drainage, which instead uses multiple directional wells—often drilled from a single pad—to provide heat.
Cold Production
CHORUS also studies and has produced many papers on a cold production method called cold heavy oil production with sand (CHOPS). When a CHOPS well is drilled, the completion is done in such a way that allows sand to be produced. Progressive cavity pumps move the sand/oil mixture to the surface. For the first phase of production, the sand cut is high. After a certain point, the sand cut begins to decrease and the percentage of oil produced increases over time.
The production increase is due to networks of channels—researchers call these “wormholes”—which form in oil sands after the cavity pumps have been operating for a certain period of time. These wormholes provide extra channels for oil to flow through. Advantages of this method are that a lower amount of energy is required due to the absence of heating, which translates into fewer greenhouse gas emissions and possibly a lower cost of operation.
Reservoir Characterization
CHORUS industry partners provide the U of C group—under the conditions of carefully written confidentiality agreements—with proprietary well logs, core samples, and seismic data, allowing graduate students and investigators to create 3D and 4D reservoir models. Contracts allow the graduate students to publish work produced using this sensitive data in graduate theses and academic journals.
CHORUS does all research using geophysical modeling software provided to them by corporate partners such as Schlumberger. Researchers are also using a software developer kit called Ocean to develop custom modules, for already-existing geophysics computer programs, that address challenges specific to heavy oil.