As today’s deep wells challenge the bounds of pressure and temperature, accurate reservoir testing has become essential to mitigate production risk. The information contained in a series of downhole pressure transient measurements and representative reservoir fluid samples can make or break a prospect’s potential.
The consistent and accurate acquisition of this information requires the precision instrumentation and functionality of a drillstem testing system. Whereas excellent downhole logging instruments can describe the near-borehole regions, only a drillstem test can reach deeply into the reservoir to discover boundaries, faults, and fractures; confirm volumetric reserves estimations; and acquire the cleanest, most representative fluid samples to provide accurate fluid phase behavior, physical properties, and compositional analyses.
Safety, Reliability, and Efficiency
The Schlumberger Quartet high-performance downhole reservoir testing system combines four proven downhole technologies into a package that can isolate the zone, control flow, measure pressure and temperature, and acquire multiple single-phase reservoir fluid samples on a single trip into the well. The system provides enhanced safety, increased efficiency, and improved reliability to testing operations.
Compared with conventional downhole test strings, the system functions with a 35% lower tool operating pressure, 50% fewer seals, and 60% fewer connections, while requiring 90% less nitrogen. The system is four times shorter than a conventional tool string because it eliminates the requirement for a safety joint, jar, slip joints, and drill collars.
Despite its smaller size, the system is sufficiently durable to permit perforating guns to be run below the packer and fired without incurring damage to the tools or impairing their accuracy or integrity. The system also includes a below-packer circulating valve to allow a more efficient well kill following the test, which is especially important when testing gas wells.
Each of the four tools that make up the downhole reservoir testing system operates individually and collectively to perform the test. The Certis high-integrity reservoir test isolation system delivers production-quality well isolation. The isolation system combines the features of a retrievable drillstem test packer with a hydraulically set permanent packer, making the safety joint, jar, slip joints, and drill collars unnecessary. Because the system is actuated by annulus pressure, no rotational or set down forces are required.
Once the packer is set, the stinger is released and the internal seals are allowed to move in the sealbore. After testing, a straight pull releases the slips and causes the packer sealing element to collapse. A bypass valve opens to prevent swabbing the well while pulling the test string out of the hole.
The IRDV intelligent remote dual valve contains the tester valve plus a circulating valve that allows communication between the test string and the annulus. Actuated by low-level pressure pulses, the tester valve and circulating valve can be operated individually or simultaneously up to a total of 24 complete (open/close) cycles. A unique built-in feature allows the mechanical override of the tool and the option of combining two dual valve tools in the same string for independent operation or pairing one valve with another for redundancy in the string.
The Signature quartz gauge precisely measures dynamic pressure and temperature and records it in nonvolatile memory for the duration of the test. The gauge’s multichip module, pressure and temperature measurement electronics, clock, and nonvolatile memory are mounted on the same ceramic substrate, which significantly improves measurement quality and suppresses drift.
The SCAR inline independent reservoir fluid sampling system collects and retrieves multiple fluid samples and maintains them at or above reservoir pressure. The system captures contaminant-free reservoir fluid samples using eight 300 cm3 Inconel fluid samplers. Each sampler is independently precharged with nitrogen for pressure compensation, enabling the retrieval of high-shrinkage reservoir fluids at or above reservoir pressure even in low-temperature operating environments such as deep water.
Samplers can be actuated simultaneously or selectively, using surface commands by means of annular pressure, and run with the latest generation inert coatings to address H2S and other challenging questions related to trace element species concentrations.
Testing the Limit
The capabilities of the Quartet system have been achievable up to a rated temperature of 350°F. To keep pace with the industry’s expansion into the environmental frontiers, the Quartet-HT high-performance downhole reservoir testing system was recently developed. The new system maintains the features of the original, but extends the pressure, temperature, and time limits of the individual tool component systems. The system incorporates the latest all-ceramic multichip module electronics (Fig. 1) and is rated to 410°F, enabling it to perform at ultrahigh reservoir temperatures.
The high-integrity reservoir test isolation system has undergone an extensive high-pressure/high-temperature (HP/HT) testing and qualification program defined by a Schlumberger proprietary pressure and temperature mission profile, including qualification at the ISO 14310 V3 grade.
In addition to delivering a much higher testing efficiency in HP/HT environments, the new system has operated safely in extreme sour gas conditions of up to 40% H2S in the Arabian Gulf.
The ceramic substrate on which the quartz gauge components are mounted allows the gauge to withstand HP/HT conditions for an extended period so that the measurement quality remains high for the duration of the test (Fig. 2).
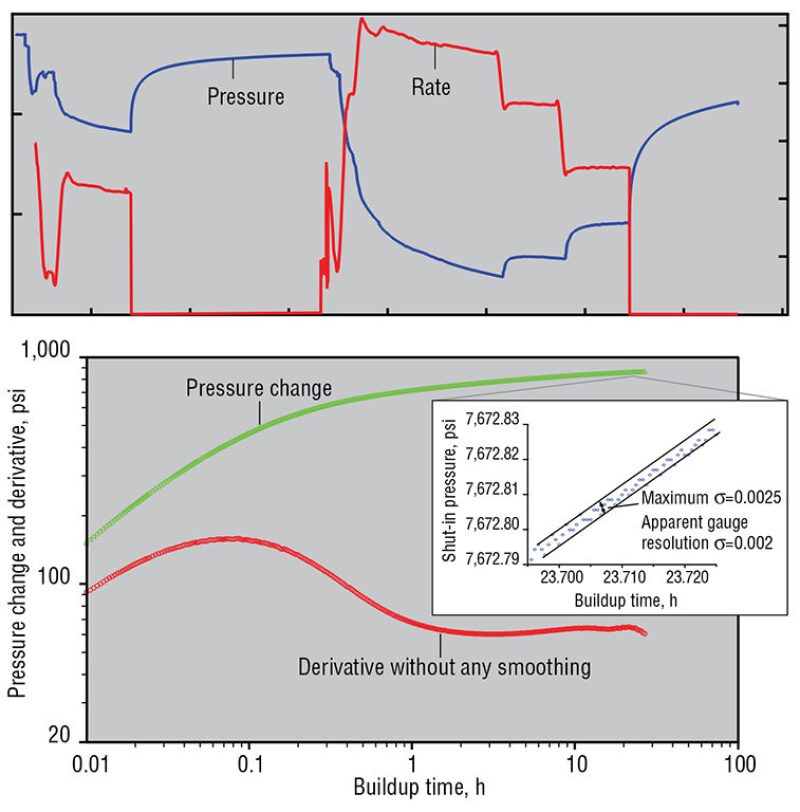
The Quartet-HT system maintains well integrity while testing safely, accurately, and efficiently at the extremes of the well environment. The multicycle and single-trip features provide operational efficiencies that can reduce rig time and risk. The HT capabilities allow operators to isolate, control, measure, and sample closer to the HT reservoir for better test results and more accurate reservoir characterization.