An increase in local gas consumption in the UAE has caused Abu Dhabi National Oil Company to turn to development of the emirate’s sour gas fields, one of the most challenging types of fields. The development of the first sour gas field here, the Shah gas field in Abu Dhabi, is on track for 2014 startup with work on the project more than 70% complete at the end of 2012.
The USD-10-billion project is proceeding under the direction of Al Hosn Gas, a joint venture between Abu Dhabi National Oil Company (ADNOC) and Occidental Petroleum Corporation (Oxy), where Oxy holds a 40% participating interest in a 30-year contract. ADNOC holds the remaining 60% interest.
“The project involves construction of several gas-gathering systems, new gas and liquid pipelines, and processing trains. The development is expected to produce significant amounts of condensate and natural gas liquids [NGL],” said Saif Al Ghafli, chief executive of Al Hosn Gas.
In 2012, Al Hosn Gas constructed plants and a pipeline network, and completed almost four of the 20 wells targeted in the drilling campaign. In addition, the joint venture took over full operatorship of the drilling program from Abu Dhabi Company for Onshore Oil Operations (Adco) in April 2012, and finalized contracting of required services and materials for the drilling program.
The joint venture also obtained two rental drilling rigs that started drilling operations in July 2012, in addition to Adco’s assistance in lending a rig and drilling the first four wells in 2011 and 2012.
Al Hosn Gas’ Development Division, which includes geologists, geophysicists, reservoir engineers, drilling engineers, and drilling health, safety, and environment (HSE) and field-implementation specialists, will help ensure that the continuously updated reservoir development and drilling plans can aid in maintaining uninterrupted availability of the anticipated volumes of gas at the wellheads during the project’s expected 30-year lifespan.
The development team conducted the first well-production test on 5,000‑ft lateral sections in the Arab C and D reservoirs in the Shah field. The subsurface group has continued to build and improve reservoir models based on the latest well data obtained to further optimize the ongoing drilling program. A seismic-data reprocessing pilot was successfully concluded, providing further technical insight for optimum well placement in the reservoir, and will move on to full field implementation later this year.
The Shah Gas Development (SGD) project consists of four major elements: the gas-gathering system, the Shah processing plant, product pipelines, and the Shah sulfur station. The field’s high hydrogen sulfide content—23% in the well fluid—means that in addition to key HSE design and implementation considerations, it will pose certain unique challenges due to the sheer scope of work to be done. The SGD project will also have a total of four trains for the massive Sulfur Recovery Units (SRU) that will process the 1 Bcf/D of sour gas. The SRUs will have a capacity of 2,500 tons per day (T/D).
The four main products expected to be produced from the billion-scf/day of feed gas at SGD, which lies about 180 km southwest of Abu Dhabi, are sales gas (500 MMscf/day), NGL (4,400 T/D), sulfur (9,200 T/D), and about 33,000 B/D of condensate.
“Considering its size, cost, and complexity, the Shah Gas Development program has really proceeded at a fairly aggressive pace,” said David Schulte, Fluor’s principal process engineer, during Dome Exhibitions’ Sour Oil and Gas Advanced Technology Conference held in Abu Dhabi in 2012. Fluor oversaw the pre-FEED and FEED stages of the SGD. “This is a billion-scf/day megaproject; this is not an incremental investment and incremental expansion; it’s an immediate step to a billion scf/day,” explained Schulte.
Necessity, Not Choice
The UAE’s largest gas reserves, estimated at 198.5 Tcf, are located in Abu Dhabi. UAE government sources estimate that such reserves, at current production will, excluding any new discoveries, last for over 150 years.
However, the data tell only half the story. Much of these reserves are inextricably linked to oil production. At the same time, most have a high sour content, making extraction and processing expensive. For example, the Khuff gas reservoir has a hydrogen sulfide content ranging between 20,000 and 200,000 ppm, a level that must be reduced to 50 ppm.
For Abu Dhabi, the development of its substantial sour gas reserves, mainly the Shah field, is a key component of the emirate’s policy to ensure there is enough gas supply to meet its growing power generation requirements. “Development of the Shah gas field is important to the economic prosperity of Abu Dhabi,” said Nora Ismagilova, business analyst at Contax Partners. “With demand for gas from utilities and other industries rising, the emirate of Abu Dhabi faces major gas supply challenges.”
The development of sour gas fields is challenging and difficult. Drilling equipment and pipelines have to be carefully insulated. Infrastructure must be able to withstand high levels of pressure. Waste processing and disposal require special attention as elemental sulfur is a byproduct.
Defying the Challenges
Rick Callahan, senior vice president–development at Al Hosn Gas, said that the main design technical challenges result from the gas and reservoir characteristics of the Shah field. The gas is extremely sour, with 23% of its content hydrogen sulfide and 10% carbon dioxide. The underground temperature and pressure are equally daunting. Downhole temperature is about 150°C and pressures are as high as 5,500 pounds per square inch. “These characteristics, in combination with the high gas-flow rates required, demand leading-edge well-component and drilling-equipment designs currently utilized in the oil and gas industry,” Callahan said.
In addition, the production of sour gas and its conversion to the usable sweet product poses technical and financial challenges, because hydrogen sulfide is toxic and highly corrosive to certain metals. Raw sour gas is generally treated at the wellhead to remove sulfur impurities.
Such problems have traditionally discouraged oil companies from exploiting such reserves, but in recent years a growing number have successfully gained experience in handling sour gas.
In December 2006, Oman awarded BP a production-sharing contract to develop 23 million m3/d of sour gas in the Makarem and Khazzan fields, at a capital cost of USD 500 million. Saudi Arabia also exploits sour gas in the Karan field.
In May 2007, the National Iranian Oil Company officially inaugurated the Amak project, which uses sour gas from the Bangestan reservoirs of the Abd-E-Teimur, Mansouri, Marun, Ahwaz, and Kupal fields. Sour gas is also extracted from Iran’s offshore territory by the South Pars Gas Complex Company. In Kazakhstan, Chevron has begun reinjecting sour gas at the Tengiz field in its drive to expand output.
For Abu Dhabi, the idea of tapping sour gas fields started in the early 1990s, after a study by the UK/Dutch Shell Group, commissioned by ADNOC, concluded that it would be technically and commercially feasible to tap sour gas from three fields: Hail, with a planned processed output of 500 MMcf/D; Shah, with 1 Bcf/D; and Bab, with 1.3 Bcf/D.
Initially this was not followed up on, as plans to import sweet gas from Qatar through the Dolphin pipeline gathered momentum. However, even before Dolphin supplies started flowing in June 2007, it was becoming clear that its capacity might be outstripped by the acceleration in Emirati demand. Industrial diversification is the biggest driver and soaring demand revived ADNOC’s thoughts of tapping domestic reserves of sour gas.
Currently Abu Dhabi pays USD 1.25 per million British thermal units to Qatar for gas from the Dolphin pipeline. The price of Abu Dhabi sour gas would be much higher. Cost of Shah Field sulfur extraction alone is estimated at four times the price paid for Qatar gas.
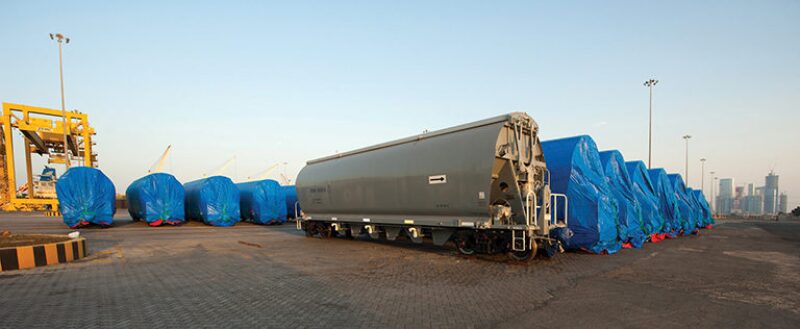
Seeking Partners
For international energy companies, high costs may not be a deterrent. They are used to operating in parts of the world where cheap energy is not the norm, and there are added incentives. Shah’s developer would establish itself as a major producer, as it would control 40% of the sour gas project, while ADNOC holds 60%.
Initially, ADNOC wanted to develop the Shah and Bab fields at a combined cost of about USD 10 billion. In April 2007, it received tenders from ConocoPhillips; ExxonMobil; Occidental Petroleum; Shell; France’s Total; BP; Japan Oil Development Company; and Wintershall, a subsidiary of Germany’s BASF, to develop the sour gas fields.
Bab was perceived by companies to be more technically complex, and therefore would carry higher production costs. Its 50% carbon dioxide content far exceeds Shah’s 23% hydrogen sulfide content, and its location in the heart of Abu Dhabi’s oil operations presents serious health and safety concerns. Bab’s gas reservoirs also contain less associated liquids and are poorer quality than Shah’s.
ADNOC then decided to set Bab aside. It invited ConocoPhillips, ExxonMobil, Occidental, and Shell to submit new bids for Shah in August 2007.
Hampered Beginning
In August 2008, ADNOC selected ConocoPhillips as a partner for the development of the Shah project, followed in July 2009 by a joint-venture and field-entry agreement. Under the deal, ConocoPhillips was going to have a 40% stake in the joint-venture development, with ADNOC to hold the remainder.
But in April 2010, ConocoPhillips decided to pull out from the project without giving details about the move. Sources based in Abu Dhabi told the Dow Jones News Service that ConocoPhillips sought to concentrate on short- to medium-term revenue growth. “The new strategic direction of the company [ConocoPhillips] is to focus more on value creation than growth; that means value for the shareholders in the short and medium term and the Shah project is a long-term contributor to value,” said a company official.
In January 2011, ADNOC selected Occidental as a partner to develop the field. Under the terms of the new agreement in principle, Oxy will hold a 40% participating interest in a 30-year contract. ADNOC holds the remaining 60% interest.
The SGD project is the most challenging project ever undertaken by ADNOC. “The extreme toxicity and corrosiveness of hydrogen sulfide, which reacts with water to form sulfuric acid, makes Shah one of the most technically challenging hydrocarbon projects ever undertaken in Abu Dhabi,” said Ismagilova. “The gas in the Shah field consists of approximately 23% hydrogen sulfide and 10% carbon dioxide.”
The remoteness of the location offers its own set of challenges as far as logistics are concerned. “Another problem is that the Shah gas field is located in a remote area south of Liwa and the gas reserve is located deep in the ground,” Ismagilova added.
In June 2007 the feasibility studies and pre-FEEDs were completed by Fluor. In February 2009 Fluor completed the FEED. In March 2010, the first engineering, procurement, and construction (EPC) package was awarded—this was for early work and went to Al Jaber. In May 2010 the EPC packages associated with the main plant were awarded to Saipem, Samsung, and Technicas Reunidas.
Originally, the concept was to transport sulfur in liquid form all the way from Shah via hot-water-jacket pipelines down to Ruwais for granulation and export. Abu Dhabi’s decision to create a national rail system, however, gave the SGD project the advantage of using railways to transport sulfur from Shah to Ruwais. Therefore, the project now has shorter sulfur pipelines—only about 11 km long—which will take the sulfur from the Shah plant to the nearby sulfur station where the sulfur is granulated, loaded on railcars, and sent down to Ruwais for export.
To use the railway, ADNOC signed a contract with Etihad Railway to build the first phase of its railway network—the 266-km Shah-Habshan-Ruwais section. The rail line will be built to transport granulated sulfur for export from ADNOC’s oil and gas fields, including Shah. The Habshan-Ruwais link is scheduled for completion by the end of 2013, and the Shah gas field-Ruwais link by the end of 2014, according to the agreement.
In early January 2013, Etihad Railway announced that the first shipment of wagons, to be used in Stage One of the rail project linking Shah and Habshan to Ruwais in the Western Region arrived at Abu Dhabi’s Mina Zayed port. The wagons’ top-hatch covers for loading maintain the purity of the sulfur at 99.9%. Furthermore, train transport allows for a capacity of up to 22,000 T/D of sulfur.
The development of the Shah gas field will also allow the UAE to increase its production capacity of sulfur to 22,000 T/D by 2015. “By 2015 the field is expected to produce around 9,200 T/D of sulfur,” said Tareq Sahoo, supervisor of operations at Adco. “Once the Shah project starts, we expect sulfurproduction in the UAE to reach 22,000 T/D,” he said.
Breathing Life Into Bab and Hail
Abu Dhabi has also recently breathed life into two shelved multibillion-dollar sour gas projects, Bab and Hail fields.
ADNOC has formally sent letters to prequalified companies for the Bab sour gas development. ExxonMobil, Royal Dutch Shell, BP, and Total were invited. South Korea’s Kogas is also potentially among those short-listed. Bids are due by the end of the third quarter.
ADNOC also sent letters to companies inviting them to submit offers for the offshore Hail sour gas field.
Hail, with 11% carbon dioxide, is less toxic than Shah or Bab, but is located in ecologically fragile shallow waters, causing ADNOC to proceed cautiously. ADNOC has previously suggested Hail could produce up to 1 Bcf/D of gas.