This case history presents the highly challenging extended-reach deepwater well, Ursa A-10, drilled in the Ursa (Latin for bear) prospect in the US Gulf of Mexico (GOM). This 30,000-ft well, drilled from the Ursa tension-leg platform (TLP) to a vertical depth of 18,000 ft and a horizontal displacement (HD) of 20,000 ft, targeted the Yellow sand in the Ursa/Princess section of the greater Mars-Ursa basin. During drilling of the original hole, a subsequent sidetrack, and two mechanical bypasses, several significant hole problems materialized that led to extensive nonproductive time. At least five independent borehole-failure mechanisms were encountered.
Introduction
In the aftermath of the tragic 2010 Macondo/Deepwater Horizon event, it is important that the industry share case studies on successful wells. It also is important to share information on wells that proved to be very challenging. Sharing learnings, best practices, and experiences on such wells will raise the overall level of proficiency in constructing these wells throughout the industry. As is often the case, more is learned from adversity than from outright success. This is the main reason that the Ursa A-10 case is presented.
Over the last decade, world-class extended-reach-drilling (ERD) wells have been drilled in the continued development of the Mars-Ursa basin in the GOM. These high-deviation wells are distinguished by depth [true vertical depth (TVD) >17,000 ft], HD ≥20,000 ft, and overall measured depth (MD) ≥30,000 ft. Challenges include a geopressured deepwater environment, complex casing programs, and special drilling issues.
The combination of these challenges makes the Ursa A-10 case noteworthy. ERD wells have been drilled to longer HD and overall MD, but those wells generally had simpler casing programs and a more-forgiving pore-pressure/fracture-gradient environment with associated drilling margins. Larger margins leave more room for such things as equivalent-circulating-density (ECD) and annular-pressure fluctuations, mud problems (such as barite sag and hole-cleaning and associated pack-off problems), accommodating manageable levels of borehole instability, and implementation of limited redesign philosophies.
Well Overview
The objective of the Ursa A-10 well was to construct a producing well in the massive Yellow sand underlying the entire greater Mars-Ursa basin, while implementing ERD from the Ursa TLP to a remote Princess target. The pore-pressure, fracture-gradient, and well-construction challenges were the result of a very narrow drilling margin, with differences between the minimum horizontal stress and the mud weight required for borehole stability being less than 1 lbm/gal at depths greater than 17,000-ft TVD. These margins were further compromised by depletion in reservoir sections that were produced previously, leading to reduced pore pressure, associated high mud overbalance, reduced minimum horizontal stress, and associated increased risks for tensile failure and induced fracturing.
The Ursa A-10 casing program (shallow strings were batch set earlier in the field-development program) involved deepening the well below the 18⅝-in. casing set at 6,131-ft MD (water depth=4,007 ft from the rotary kelly bushing, 3,800 ft from mean sea level). Although the original hole of the Ursa A-10 did reach its intended target and total depth (TD) of 30,100 ft, unfortunately the well was lost after severe lost circulation caused by fractures at the base of the Yellow sand, and because of subsequent borehole-instability problems that led to an irreversible stuck-pipe event. The subsequent sidetracks and bypasses never reached the intended Yellow sand target. Trouble costs exceeded 40% of overall well cost.
Ultimately, the Ursa A-10 ST2 well was drilled to, and completed in, the shallower Above Magenta sand, which was a secondary target. When brought on production, the well was a prolific and steady producer, with initial oil production of approximately 30,000 B/D—one of the best and most profitable Ursa wells.
Drilling History and Drilling-Problem Overview
Before constructing the Ursa A-10, ERD had proved challenging in offset wells. Problems became severe while drilling the Ursa/Princess A-10 well, which was drilled from the Ursa TLP to a Princess target, as shown in Fig. 1.

Well Princess MC765-1, a near-field exploration well, and the original Princess discovery well, was drilled as a subsea well from a floater, with no evidence of borehole instability. The main problem on this well was induced lost circulation, caused mainly by hole-cleaning inefficiencies, leading to pack-off problems and associated ECD spikes that triggered wellbore tensile failure. Losses were dealt with effectively by use of routine lost-circulation pills. Trouble cost represented only 9% of overall well cost, an excellent result. Geological sidetracks were drilled from Well MC765-1 to further delineate the prospect. Wells MC765-1 ST1 and MC765-1 ST2 were lost as a result of poor hole cleaning from inadequate annular velocities and poor hole-cleaning practices. Borehole breakout was noticed on these wells, which exacerbated the hole-cleaning problems by reducing annular velocities (larger effective hole diameter) and delivering large shale fragments to the annulus. A third sidetrack (Well MC765-3) was drilled successfully to TD, evaluated, and cased by paying particular attention to hole cleaning and to preventing pack-off events. Trouble cost for the sidetracking campaign totaled 35% of overall well cost.
Drilling experiences for the various hole sections of the Princess MC766-1 appraisal well were related to hole cleaning and occurred throughout the well but always proved to be manageable and, ultimately, did not compromise the objectives of the well, which was drilled to TD and evaluated (with a trouble cost of 28% of total well cost). The relatively positive experience of the MC765 and MC766 wells led to the plan to drill the next Princess well from the available infrastructure of the Ursa TLP, with associated lower unit costs. This change required drilling a 20,000-ft horizontal step out with relatively large-diameter hole sizes to a remote target. The TLP rig systems (e.g., hoisting capability and pump capacity) had lower capacities than the floater. These factors and limiters proved to be important for the Ursa A-10 well.
The Ursa A-10 original hole experienced zonal-isolation problems at its shallow casing strings, requiring cement squeezes on both the 16- and 13⅝-in. casing shoes. Heavy mud losses were observed while drilling the production hole close to TD. These mud losses were suspected to have originated at the previous casing shoe. Upon the trip back to the casing shoe (with the intent to treat it locally for lost circulation), the rig experienced a lightning strike and was disabled for a week while repairs were made to the draw works and the topdrive system. During this time of inactivity, the string became stuck in hole. The drillpipe and bottomhole-assembly components were only partly recovered in the subsequent fishing exercise, and the well was sidetracked around the remaining fish. Subsequent analysis of recorded time-lapse resistivity showed the cause of the lost-circulation event to have been at the base of the Yellow sand rather than at the casing shoe: The resistivity signal during the wipe showed the characteristic invasion of high-resistivity synthetic-based mud (SBM) into a natural- or induced-fracture system. Note that encountering fractures (either natural or induced) at the top or base of clastic reservoirs in the GOM is common. These detachment zones combine a shale characteristic (low strength) with a sand characteristic (low stress), an environment ideal for tensile failure and fracture opening.
The Ursa A-10 ST1 sidetrack was drilled with a mud weight that proved insufficient for borehole stability. The well suffered from hole-cleaning, pack-off, and string-sticking problems. A minimum mud weight of 13.0 lbm/gal was required for borehole stability. During drilling, the dynamic circulating pressures lifted the ECD above the minimum-mud-weight requirement, and, during connections, the static mud weight fell only slightly (by 0.1 to 0.2 lbm/gal) below the recommended mud-weight value. During the trip out of the hole, the first 700 ft were backreamed, with ECDs sufficient to stabilize the hole. From 16,400‑ft TVD upward, however, the string was pulled dry, and the combination of swabbing and barite sag lowered the effective mud weight below 12.5 lbm/gal, insufficient for borehole stability. The resulting instability was indicated on the caliper log, which showed the 12¼-in. hole enlarged by more than 10 in. in several sections. A 10⅛×9⅝-in. liner was run in the section and became stuck high, at 16,635‑ft TVD (26,710-ft MD), presumably because of poor hole gauge and obstructions (cuttings and cavings beds) still in the hole. After drilling out and experiencing an unmanageable combination of borehole instability, packoff-induced losses, and pipe sticking with clear signs of severe barite sag (lightweight mud returns to surface), the well was plugged back with cement.
The Ursa A-10 ST1 BP1 and BP2 bypasses were drilled with an improved mud weight of 13.0 lbm/gal and with partially successful attempts to control barite-sag problems. This led to a noticeable improvement in borehole caliper. However, both wells experienced severe wellbore instability, packoff, and stuck pipe in what, at first, appeared to be a massive shale zone at approximately 17,500-ft TVD. Fig. 2 a and b show, respectively, an interpretation of the brittle fractured interval and one of the large blocky shale fragments recovered from this zone. Fig. 3 shows that noticeable invasion of SBM occurred in this zone, uncharacteristic behavior for shale, which typically prevents SBM invasion because of high capillary-entry pressure. The invasion pattern was attributed to the presence of microfractures in a brittle-shale zone, which destabilizes when SBM invades along the fracture planes and equilibrates wellbore pressure and pore pressure. It proved impossible to control the wellbore problems, and the wells were plugged back and sidetracked.

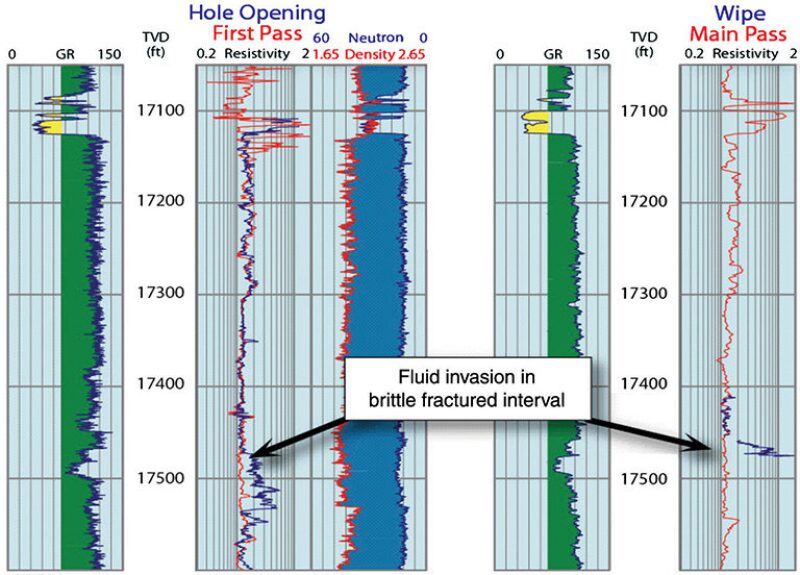
The Ursa A-10 ST2 well was drilled to the revised target in the Above Magenta sand. Care was taken to drill the well with the appropriate overbalance (i.e., borehole support) while attempting to minimize invasion in the brittle fractured-shale zone by keeping lost-circulation bridging materials in the mud continuously and tightening fluid-loss control. Also, annular-pressure fluctuations, which could destabilize the fractured-shale zone, were controlled as much as possible. The well did experience a lost-circulation event upon penetrating the Above Magenta sand. This event was never explained fully, but may have been related to the lateral effect of the problems that had occurred on the previous penetrations.
Drilling-Problem Analyses
The failure mechanisms experienced on the various Ursa A-10 wells had multiple causes, some of which acted on all of the wells (such as barite sag) while others were unique to particular wells (e.g., failures caused by SBM invasion into the fracture planes of the brittle shale). Detailed analyses were carried out by a multidisciplinary team with expertise in drilling operations, petrophysics, and drilling-fluid chemistry. Industry experts were consulted also. These analyses are detailed in the complete paper.
Borehole Instability and Lost Circulation. Borehole problems materialized in several forms on the Ursa/Princess wells. Five distinct failure mechanisms were identified.
- Shear failure because of insufficient mud-weight support
- Anisotropic failure in a fractured shale
- Tensile failure and fracture opening in intact rock
- Fracture reopening in naturally fractured rock
- Wellbore fatigue caused by stress cycling
Barite Sag. Sag is the undesirable variation in drilling-fluid density caused by downhole settling of weighting material, mostly in muds at densities greater than 12 lbm/gal. Sag can cause serious drilling problems (e.g., well-control incidents, borehole instability, formation breakdown, and lost circulation), especially in high-pressure/high-temperature wells and wells with deviation >30°, particularly ERD wells. There are two forms of sag: static sag (settling correlated with gel strength of the mud) and dynamic sag (correlated with ultralow-end rheology of the mud).
Hole Cleaning. Hole-cleaning problems occurred in all Ursa/Princess wells. They were directly responsible for the loss of two sidetracks in Well MC765-1 and hindered progress in all of the Ursa A-10 wells. The latter suffered from the challenge of having to clean high-deviation long-reach wellbores that were no longer stable (delivering large-sized cavings to the annulus) and were continually enlarging (thereby reducing annular velocities critical to good hole-cleaning efficiency). To clean these ERD wellbores effectively, traditional practices (derived from drilling near-vertical wells) must be abandoned and practices must be adopted that address the challenges of ERD at high deviation. In the aftermath of Well Ursa A-10, a hole-cleaning best-practices document was assembled.
Conclusions
- Deepwater ERD wells in the Mars-Ursa basin present significant drilling challenges. Understanding and addressing these challenges carefully is the key to success.
- For the Ursa/Princess wells, it is crucial that the available drilling margin be well-understood and that ECD be managed properly throughout all drilling operations.
- All team members should realize that extra time may need to be spent on special practices (e.g., hole-cleaning cycles) to avoid drilling problems. The extra time is not wasted and does not conflict with technical-limit drilling objectives. The phrase “Sometimes one must go slow to go fast” describes this strategy best.
Specific recommendations for Ursa/Princess ERD wells include:
- Understanding and managing rig limitations
- Optimizing drilling practices and abandoning outdated practices (e.g., pumping sweeps for ERD hole cleaning)
- Updating best practices (including for hole cleaning, barite sag, and leakoff testing)
- Active use of real-time mud-logging, measurement-while-drilling, logging-while-drilling, and pressure-while-drilling data to characterize the hole condition and to formulate remedies (e.g., for barite sag and hole instability) if necessary
- Use of new technologies (e.g., sag-resistant flat-rheology SBM) as enablers.
The need for good communication and buy-in of the drilling plan and associated recommended practices by all stakeholders, ranging from the asset manager in the office to roustabouts on the rig, cannot be overstated.
This article, written by Senior Technology Editor Dennis Denney, contains highlights of paper SPE 163525, “Setting Free the Bear: The Challenges and Lessons of the Ursa A-10 Deepwater ERD Well,” by John Gradishar, SPE, and Gustavo Ugueto, SPE, Shell Upstream Americas, and Eric van Oort, University of Texas at Austin (formerly with Shell Upstream Americas), prepared for the 2013 SPE/IADC Drilling Conference and Exhibition, Amsterdam, 5–7 March. The paper has not been peer reviewed.